Tailored Product Packaging Equipment Fixing Solutions to Suit Your One-of-a-kind Business Needs
In today's affordable market, organizations have to guarantee their product packaging procedures run effortlessly, and tailored repair service solutions for equipment are pivotal in attaining this. These bespoke solutions provide to the distinct demands of each company, dealing with particular functional challenges and enhancing equipment performance. By integrating top quality products and strategic upkeep methods, companies can substantially decrease downtime and costs. What are the vital components that make these solutions vital, and just how can services purposefully select suppliers that align with their long-term objectives? This conversation aims to discover the nuanced advantages of tailored repair service strategies.
Recognizing Your Equipment Needs
To efficiently address the repair and maintenance of packaging devices, it is extremely important to obtain a comprehensive understanding of your equipment needs (packaging equipment repair services). This includes analyzing the particular kinds of equipment being used and recognizing their duties within your manufacturing line. Identifying these aspects enables you to prioritize upkeep jobs and allot resources successfully, reducing downtime and ensuring smooth procedures
An in-depth stock of your equipment, including make, upkeep, age, and design background, develops the keystone of this understanding. This information helps with notified decision-making regarding fixings and upgrades, making sure that treatments are both timely and affordable. In addition, recognizing the functional needs put on each tool assists in forecasting damage patterns, thus making it possible for more exact organizing of preventative upkeep.
Teaming up with knowledgeable technicians who can offer skilled evaluations and referrals is likewise crucial in refining your tools management approach. Eventually, a comprehensive grip of your equipment needs not only enhances performance yet likewise extends the lifespan of your machinery, protecting your investment.
Advantages of Personalized Repair Work Solutions
Custom-made fixing solutions provide a tailored approach to fixing and keeping product packaging equipment, making sure options that fit the special demands of each business. This bespoke strategy gives myriad benefits, boosting operational performance and reducing downtime. By recognizing the certain equipment and procedures of a firm, tailored services can deal with problems better than generic solutions, guaranteeing that repair services are aligned with operational objectives and workflow dynamics.
Moreover, these solutions promote better resource management. Tailored fixing plans assist forecast upkeep demands, enabling services to designate resources more effectively and decrease unforeseen prices. This positive strategy not just extends tools lifespan yet also enhances performance, stopping regular failures and cultivating a much more reliable manufacturing atmosphere.
As packaging innovations advance, having a repair service attuned to a business's distinct configuration ensures fast adjustment to brand-new devices and procedures. Furthermore, individualized solution cultivates a more detailed relationship with repair work service providers, ensuring quicker feedback times and even more effective interaction, inevitably leading to enhanced solution high quality and company growth.
Key Parts of Tailored Solutions
A well-crafted customized solution for product packaging equipment fixing is built on several essential components that make sure performance and reliability. A detailed analysis of the tools is important. This entails diagnosing the origin of any kind of operational issues and comprehending the specific requirements of the machinery, which lays the foundation for creating a specific repair work method.
Secondly, using top quality, suitable components is paramount. Picking elements that line up with the original tools requirements not only enhances capability however also extends the life expectancy of the machinery. This interest to information lessens the danger of future breakdowns and guarantees smooth procedure.
One more vital element is the execution of a customized upkeep plan. packaging equipment repair services. Regular assessments and safety nets tailored to the devices's distinct needs can dramatically try here reduce downtime and enhance performance
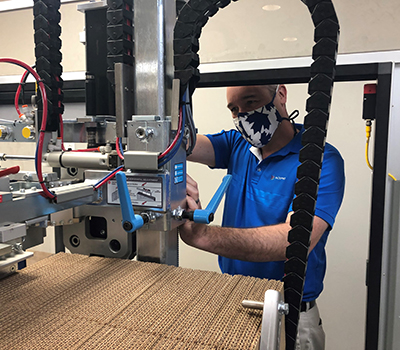
Including these elements right into a tailored repair work option not just addresses immediate issues yet additionally supplies lasting advantages, boosting total productivity and cost-effectiveness for organizations.
Choosing the Right Provider
Picking the appropriate company for packaging devices repair service is a vital decision that can substantially affect a business's operational efficiency and expense monitoring. A dependable provider ensures timely fixings and maintenance, decreasing downtime and avoiding possible production delays. When selecting a company, businesses ought to think about several important variables to guarantee they choose a companion that lines up with their particular demands.
To start with, expertise and experience in taking care of comparable equipment are important. A service copyright with a proven track document in the packaging sector can supply solutions and insights customized to one-of-a-kind business difficulties. Referrals and study from previous customers can provide valuable evidence of their capabilities.
Secondly, examine the supplier's responsiveness and accessibility. packaging equipment repair services. An optimal companion needs to supply adaptable service alternatives, including emergency situation repair solutions, to attend to immediate demands without delay. This makes certain marginal disruption dig this to procedures and preserves efficiency levels
Furthermore, think about the range of services offered. A comprehensive service provider must not only provide repair services however additionally preventive maintenance and technological assistance. This alternative strategy can enhance processes and foster lasting collaborations.
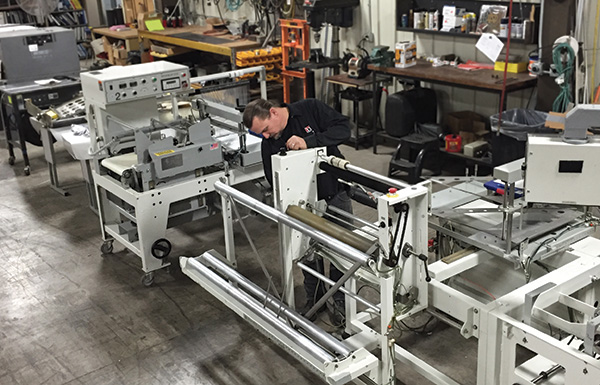
Making Best Use Of Tools Life Expectancy
Reliable equipment upkeep approaches are as vital as selecting the best provider when it pertains to maximizing the lifespan of product packaging equipment. Routine upkeep, when executed appropriately, expands the functional life of equipment by avoiding unexpected break downs and reducing repair service prices. This involves applying an organized upkeep routine that includes regular examinations, timely lubrication, and replacement of damaged components. Such aggressive steps guarantee that equipment functions at peak performance, consequently reducing the risk of costly downtime.
This not only improves the lifespan of the equipment however likewise improves total performance. These logs supply understandings right into reoccuring problems and help in planning future upkeep tasks a lot more successfully.
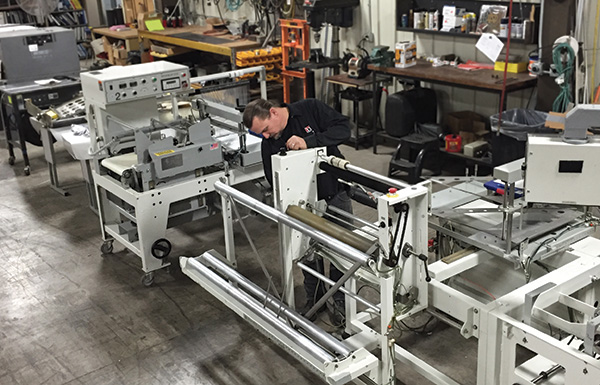
Final Thought
Customized packaging equipment repair service services play a critical duty in enhancing functional performance and decreasing downtime by aligning repair work with certain process dynamics. These customized options utilize top notch, suitable components and positive upkeep strategies to extend equipment life expectancy and maximize performance. By fostering close relationships between services and provider, tailored services enhance solution top quality and lower prices. Picking the appropriate supplier makes certain the effective application of these services, eventually causing considerable long-term advantages for companies.
In today's competitive market, businesses must guarantee their product packaging operations run seamlessly, and customized repair service solutions for equipment are pivotal in accomplishing this.To effectively resolve the fixing and maintenance of packaging tools, it is critical to get a thorough understanding of your devices needs.Customized fixing solutions provide a customized method to fixing and preserving packaging equipment, making certain options that fit the special requirements of each service.Efficient equipment maintenance methods are as crucial as picking the right solution supplier when it comes to making best use of the life expectancy of product packaging devices.Tailored product packaging equipment repair work services play an important function in enhancing functional efficiency and reducing downtime by straightening repairs with specific workflow characteristics.